Hints & Tips
The True Cost Of Jobsite Damage: Why Prevention Is Better Than Repair
April 3, 2025
In the fast-paced world of construction, jobsite damage can quickly escalate from a minor hiccup to a major financial setback. Each damaged floor, shattered window, or scratched bathtub comes with a price tag—one that encompasses not only monetary costs but also time lost, decreased productivity, and strains to your reputation. Understanding the true cost of jobsite damage is crucial for contractors, project managers, and workers alike. While repairs may seem manageable in the moment, the ripple effects can linger long after the dust settles.
Today, we delve into the importance of proactive measures that prevent damage before it occurs, highlighting how investing in preventive strategies not only shields your bottom line but also cultivates a safer and more efficient work environment. By prioritizing prevention, you pave the way for smooth operations, enhanced team morale, and a solid reputation—making it clear that, in construction, prevention is undeniably better than repair.
Understanding Jobsite Damage
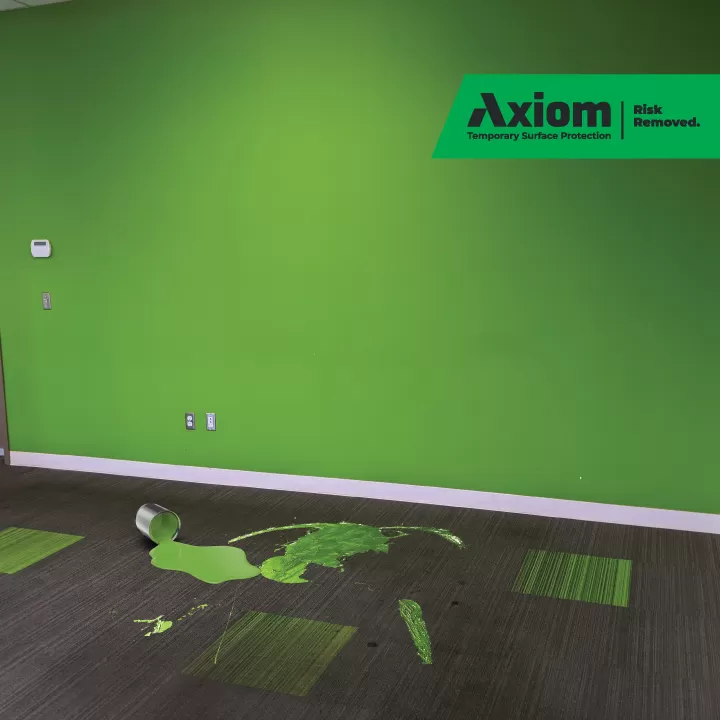
Jobsite damage in the construction industry can manifest in numerous forms. Physical damage to the structure, such as broken windows, scratched floors, and chipped countertops often occur during the transportation of materials, the use of heavy machinery, or the movement of workers across the site. Environmental damage can also be a concern, including water damage from leaks or flooding, and deterioration from exposure to harsh weather conditions. Each type of damage requires specific attention and mitigation strategies to prevent further complications.
Understanding the root causes of jobsite damage is essential for developing effective prevention strategies. By identifying the common types and causes, construction professionals can implement targeted measures to reduce the occurrence of damage. This includes investing in quality surface protection materials, which safeguard vulnerable areas from damage, ultimately saving time and money in the long run.
The Financial Impact Of Jobsite Damage
The financial implications of jobsite damage impact both immediate costs of repairs and replacements and beyond. Every instance of damage can lead to significant delays in the project timeline, causing a ripple effect that impacts the overall budget. For example, if a floor is damaged during construction, not only does it need to be repaired or replaced, but the work in that area must be halted. This delay can disrupt the workflow, affect the scheduling of subsequent tasks, and lead to increased labor costs as workers wait for the damage to be addressed.
Moreover, jobsite damage can lead to additional indirect costs. One of the most substantial is the potential for lost productivity. When workers are preoccupied with rectifying damage, they are diverted from their primary tasks, leading to inefficiencies and reduced output. This diversion not only affects the immediate work but can also have long-term effects on the project’s completion. Additionally, recurring damage issues can demoralize workers, leading to decreased morale and motivation, which further impacts productivity and job satisfaction.
The financial impact is not limited to direct and indirect costs. The reputation of a construction company can suffer significantly from frequent jobsite damage. Clients and stakeholders expect projects to be completed on time and within budget, and recurring damage issues can erode their confidence. Negative word-of-mouth, poor reviews, and damaged relationships with clients result in a reputation for poor jobsite management. This reputational damage leads to lost business opportunities and decreased competitiveness in the market. Therefore, temporary surface protection is necessary for mitigating both current and future financial issues on the jobsite.
Axiom’s Surface Protection Solutions
The most effective way to mitigate jobsite damage is by employing high-quality surface protection solutions, which is why we offer a range of products designed to safeguard various surfaces during the construction process. Our products, many of them reusable, offer high-quality protection so that your short term investment saves you money in the long run.
From high-end tile and expensive bathtubs to luxury hardwood and more basic surfaces, we’ve got the product to ensure you won’t end up paying for unnecessary repairs and extended timelines further down the line.
Some of our top products include:
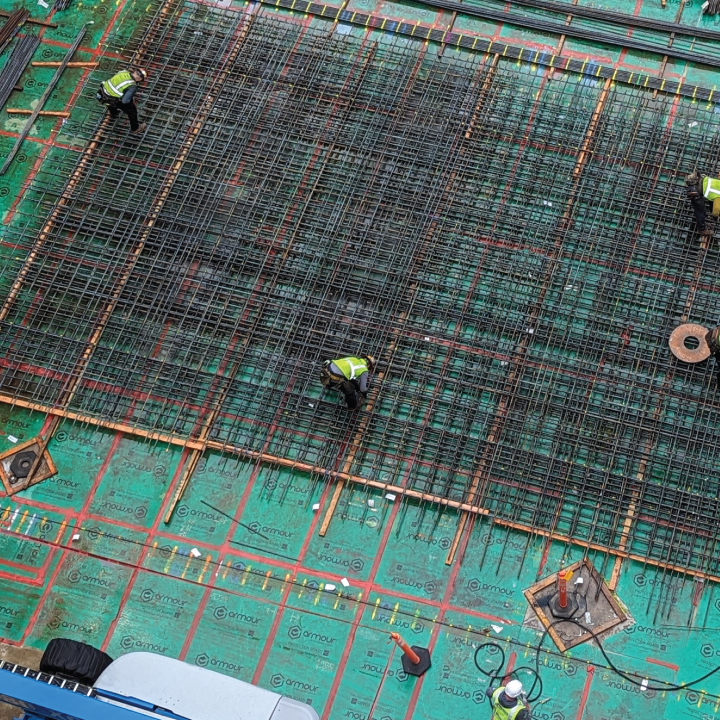
The Armour Protection Board line, made up of varying thicknesses and levels of impact resistance, are ideal for protection a variety of surfaces. From Armour Protection Board – Black, which is perfect for protecting countertops, doors, showers, and more, to Armour Protection Board – Green HD, which is the ideal plywood alternative thanks to its extreme impact protection and fleece underside, the Armour Protection Boards are the ideal solution to many surface protection scenarios.
Bulldog Board Temporary Floor Protection
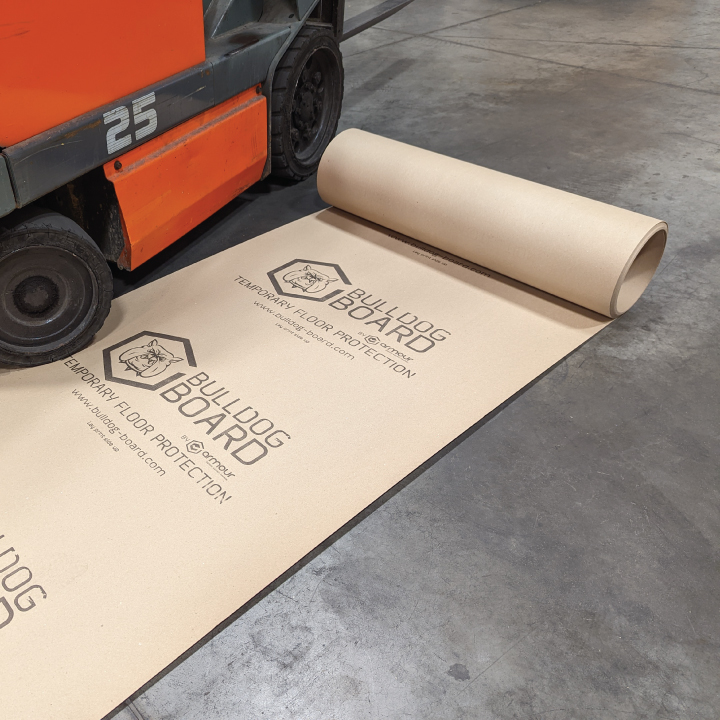
It’s no wonder that Bulldog Board has gained a reputation in the construction industry as a reliable, high-quality floor protection solution. It is durable, water-resistant, and easy to install, making for a quick and effective protection solution.
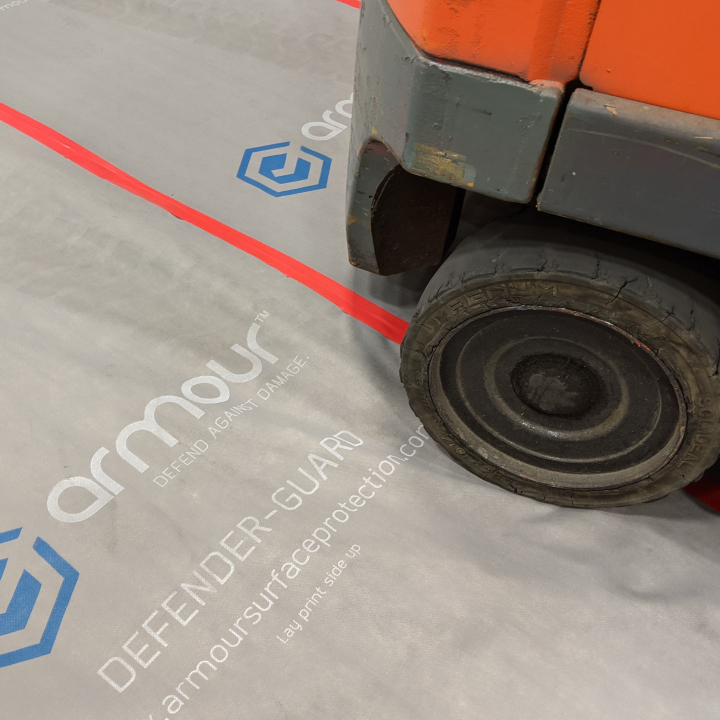
For high-strength floor protection, you can’t go wrong with the Armour Defender-Guard. Ideal for protecting hardwood, tile, laminate, and vinyl floors, the Defender-Guard is completely waterproof, tear-resistant, and lays down flat every time, so you don’t have to worry about moisture damage and more on your high-end floor surfaces.
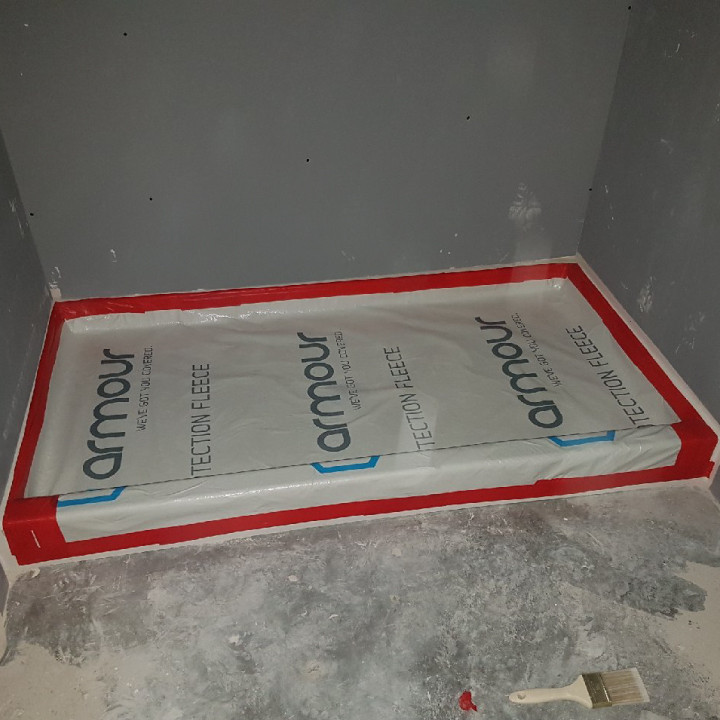
The Armour Protection Fleece is a powerhouse in the world of temporary surface protection. From floors to countertops to shower bases, the fleece provides breathable, waterproof, and non-abrasive protection from prevents scuffs, scratches, and worse.
Armour Bathtub Protection Cover
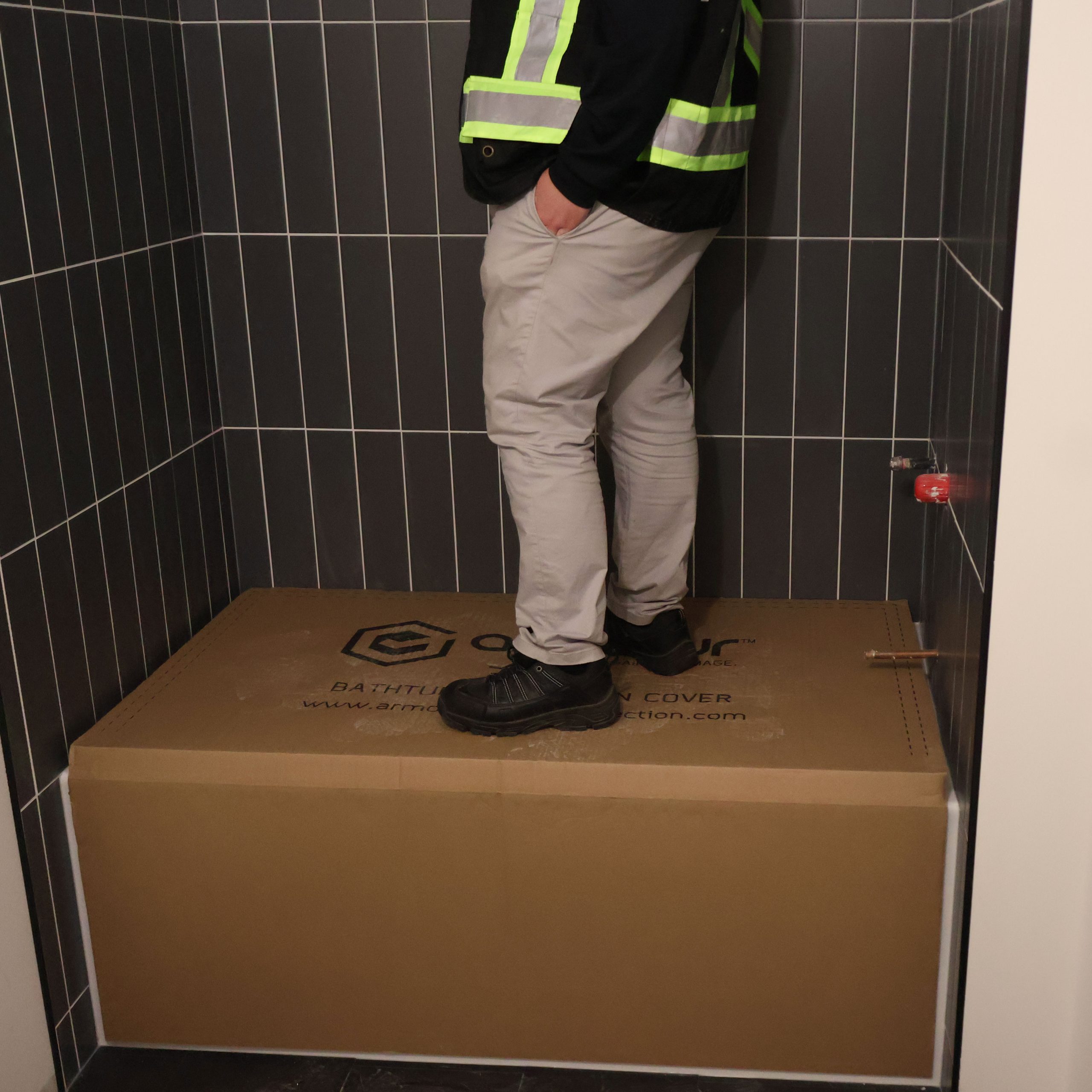
With a weight capacity of 750+ lbs, the Armour Bathtub Protection Cover is ideal for protecting bathtubs on residential construction projects. It features a pre-formed cover that protects the front of your tubs in addition to its heavy-duty cardboard top that allows work to continue on and around the tub.
Conclusion
The true cost of jobsite damage extends far beyond the immediate financial burden of repairs and replacements. It encompasses delays, lost productivity, and reputational harm that can ripple throughout a project, causing long-term consequences. By prioritizing prevention through high-quality surface protection solutions, construction professionals can avoid these hidden costs and ensure smoother operations. Investing in the right protective measures not only safeguards your budget but also enhances safety, morale, and efficiency across the entire jobsite. When it comes to construction, prevention truly is better than repair, and the payoff is well worth the effort.
Reach out today to learn how we can help you save money on your project:
- Phone: 1-866-617-8502
- Email: sales@axiomtsp.com
- Address: 125-5305 McCall Way NE, Calgary, AB T2E 7N7
- Get a Quote: Request a Quote